Un directeur général de laminoir s’est réveillé un matin avec la triste et choquante nouvelle qu’un de ses ouvrier était finalement décédé après une maladie dont l’origine officiellement reconnue était l’exposition récurrente à un solvant halogéné.
Cet ouvrier travaillait dans l’équipe de maintenance des outils qui se trouvaient à la fin de la coulée continue et qui donnait forme à la production de ce laminoir.
Une partie de cet outillage était fixe devait être nettoyé sur place rapidement, parce qu’il n’y avait que vingt minutes d’arrêt entre deux coulées. L’autre partie était mobile et était nettoyée en atelier dans des bacs-éviers. Les ouvriers de maintenance nettoyait les parties mobiles, les avant-bras plongés jusqu’au coude dans le solvant en question et décrassaient avec des tampons ferreux les pièces qui avaient pris l’huile à quelques centaines de degrés, les résidus de coupe, la calamine, etc.
Dés leur deuxième année d’activité, tous les ouvriers de cette équipe voyaient apparaître différentes maladies dont personnes ne semblaient comprendre l’origine, ou dont personne n’osait expliquer l’origine.
Tant et si bien qu’un jour, « le vieux » comme ses collègues l’appelaient, cet ancien de l’équipe, celui qui plongeait joyeusement les deux mains dans le fût de solvant pour se les nettoyer en fin de journée, manqua définitivement à l’appel.
A cette époque, je m’interrogeais quant à mon avenir professionnel. Et je m’intéressais à ces solvants que la littérature professionnelle mettait au pilori, mais qu’on trouvait toujours dans tous les ateliers de maintenance mécanique. D’une part, ils étaient interdits sauf à protéger efficacement les utilisateurs, et, d’autre part, la réalité du terrain semblait ignorer complètement ces messages alarmant.
Par un concours de circonstances dont seul le Destin a le secret, c’est à cette époque que je rencontrais le directeur de production de ce laminoir. Il me donna en quelque sorte l’ordre de trouver un substitut à ce solvant halogéné apte à satisfaire les exigences opérationnelles d’un laminoir.
Remplacer un solvant dangereux
Pour remplacer un produit dangereux, il faut que :
- Le substitut satisfasse aux exigences de l’opérationnel.
- Le substitut ne coûte pas plus cher que le produit à remplacer. Si possible, il coûtera moins cher. Même la santé des ouvriers a un prix.
- Le substitut sera conforme aux règlements. Euh! Y aurait-il des produits chimiques dans nos entreprises qui ne le seraient pas ?? Fermons la parenthèse avant qu’il ne fasse trop frais 😉
- Et surtout, il faut que les utilisateurs acceptent de changer quelque chose dans leur habitudes et, en particulier, acceptent de travailler avec un autre produit, et peut-être d’une autre manière. Et c’est là que la vraie difficulté surgit. Changer de produit, même s’il s’agit d’un poison implacable, c’est le plus difficile !
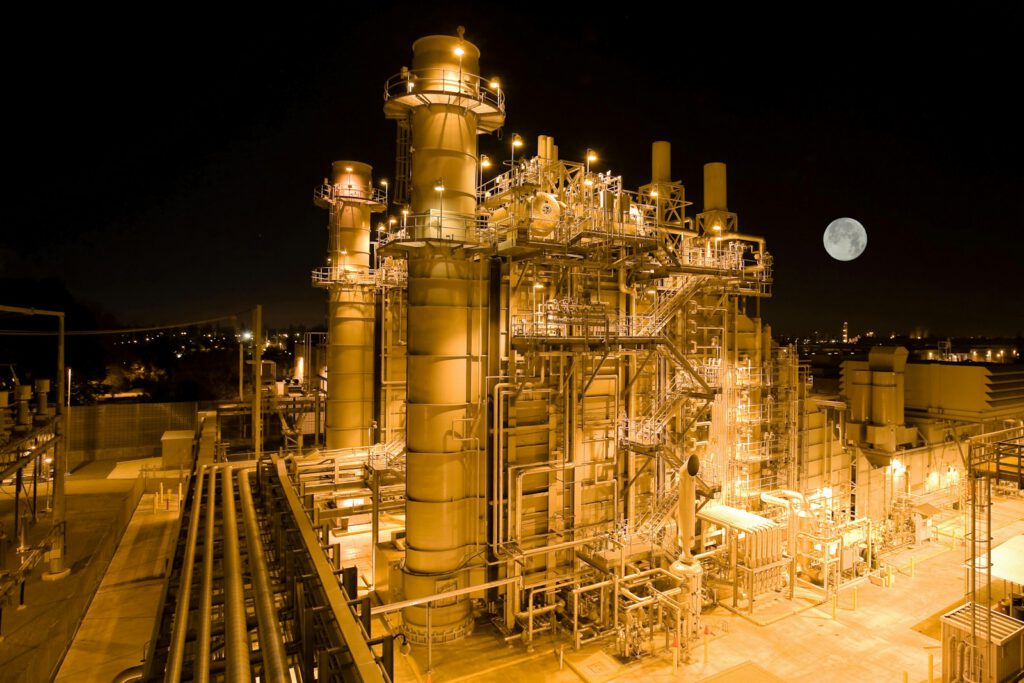
Où trouver la solution ?
Les solvants arrivent après la deuxième guerre mondiale, avec le coca-cola et le chewing-gum. Ils sont efficaces. Ils sont bon marché. Ils représentent la modernité ! Et c’est un succès qui ne se démentira pas, et jusqu’à aujourd’hui.
L’idée fut de regarder dans le passé. La métallurgie industrielle telle que nous la connaissons naît autour du début du dix-neuvième siècle. On a donc dégraissé sans solvant pendant un siècle et demi.
Si on consulte les mémoires des ingénieurs métallurgistes de cette époque on retrouvera les principes chimiques utilisés. Même si on les a oubliés.
Evidemment 80 ans de travail au solvant a aussi dissous la mémoire de nos contemporains.
Et si beaucoup de circonstances ont changé depuis cette époque ancienne, en particulier sur la structure de coûts, sur la concurrence, sur l’évolution de nos machines, les principes chimiques restent toujours valables aujourd’hui.
Retour à la base
Un dégraissant est un produit permettant d’enlever toutes traces de graisses et d’huiles d’une pièce.
Les graisses sont insolubles dans l’eau.
Pour les éliminer, on peut :
- les dissoudre (opération de dissolution), en utilisant un solvant ;
- les transformer en savons solubles dans l’eau, en utilisant des produits fortement basiques comme la soude, la potasse ou les silicates de sodium. Les graisses ont été saponifiées ;
- les décoller et les empêcher de se redéposer, en utilisant des tensioactifs, pour former une émulsion.
La solution
On comprend donc qu’on peut se passer de solvant et utiliser deux autres grandes méthodes : saponifier et émulsifier.
Il ne restait plus qu’à trouver la formule qui permettait, sans solvant, de créer un concept assez puissant pour satisfaire au sévère cahier des charges des industries métallurgiques, mais également le plus inoffensif possible pour les ouvriers, et pour l’environnement qui est devenu aujourd’hui un enjeu majeur.
C’est ainsi qu’est né
le concept Safe-T-Clean